半導體行業解決方案
原先在工廠的無塵生產車間里,工作人員需要“全副武裝”進入車間往返運送資材和完成品,以免電子元件受污染物損害,除此以外,運輸用的車輛設備往往也是一個容易被忽視的污染源,易對電子元器件產生影響。同時因為生產機臺多,人員轉運不夠及時,成本較高,還有現場通道狹窄,環境復雜人員流動大,運送種類多樣且復雜等問題。
基于這些要求,我們提供了使用MiR100+定制化料車設計+WiFi網絡部署的解決方案,在工廠無塵車間部署了2臺MiR100自主移動機器人,以優化內部物流運輸體系,加強運輸安全,提升工作效率。
在此之前,工廠車間工作人員通過多次往返進行資材及完成品的運輸;而在部署MiR100自主移動機器人解決方案后,車間內部不僅有效實現了自動化運輸,保證車間運輸安全,更減少了80%的搬運人力成本,將人力資源發揮至更具價值的工作崗位,進而使工廠實現降本增效的運營。
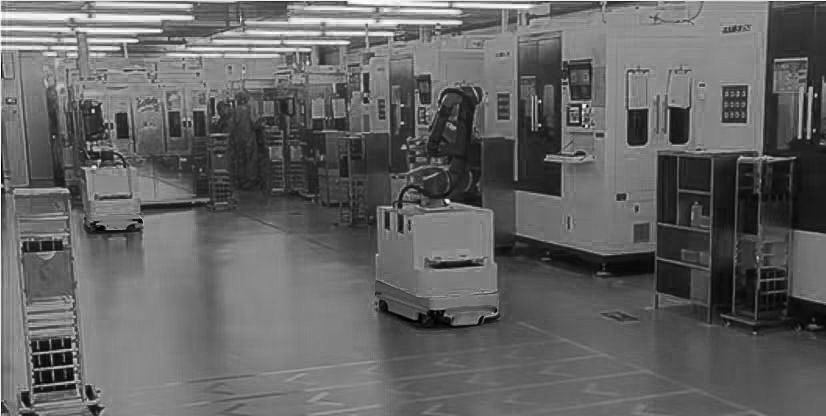
機床看護
金屬加工行業生產環境差,用工難、招工難,產線改造空間有限,傳統大型工業機器人部署困難,成本高。協作機器人不僅可以提高生產效率,保障員工安全,同時能幫助客戶應對小批量、多批次的生產挑戰,創造更可觀的長期收益。
機床加工上下料各工藝段品種多,操作重復度高,人工操作效率和準確度低。
車間作業空間一般都比較狹小,使用傳統自動化設備需要在每個機床上固定,空間占用大,一旦固定,后續改造產線耗時耗力。
協作復合機器人方案可以有效解決以上這些痛點問題。一臺復合機器人支持 12 臺機床的上下料,大幅提升生產效率,同時可節省 6 名人力。
搭載的協作機器人,采用雙電動夾爪,取料、放料一次性完成。結合 2D 視覺定位與糾偏技術,可確保每次上下料準確。切換生產品種時,在軟件中簡單設置參數即可完成。
機器人可部署于機床,實現金屬工件輸送、換料、加工、下料的全自動化,一臺機器可管理多臺機床,24 小時作業,有效節省人力成本。
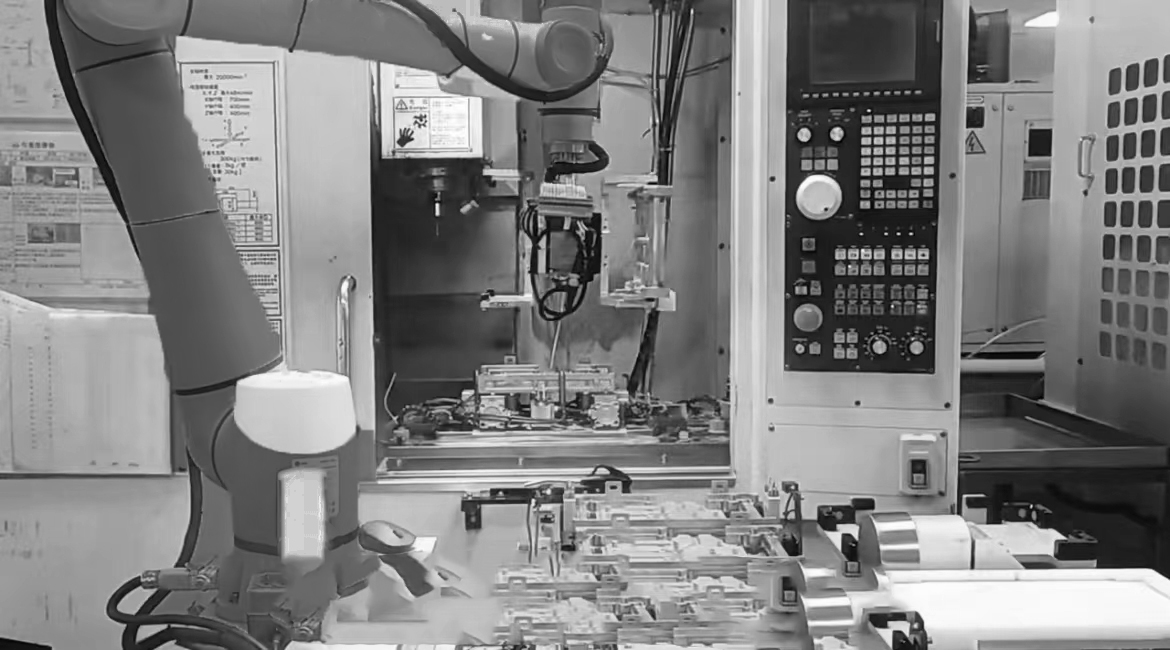
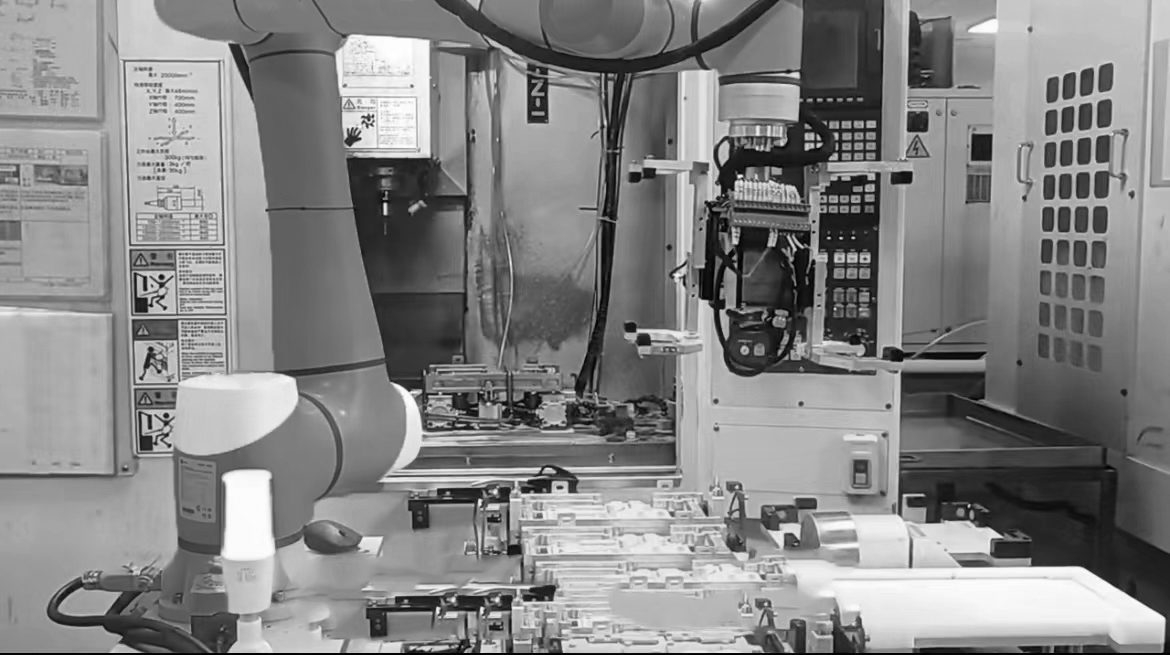
協作機器人碼垛案例
在制造業生產線的末端,有非常多的碼垛場景。這些任務在智能制造出現之前,需要人工不斷地彎腰、伸手和舉重——造成了員工重復性重型勞動的勞損風險,可能導致健康問題。
隨著智能制造的升級,碼垛成為了協作機器人重要的應用之一——不僅可以緩解員工的體能壓力,保護員工的健康,還可以讓他們從事更有創造力的角色,提升整個生產線的產能價值。
與需要大量編程的傳統機器人不同,操作協作機器人的碼垛搬運,甚至不需要任何編程基礎,利用內嵌的操作模塊選項,即可快速直接地進行各種參數設置。
“協作機器人的組合,讓你只需打開碼垛界面,輸入箱子的尺寸、重量和碼垛模式,然后按開始,機器人就會自動完成碼垛?!?/span>
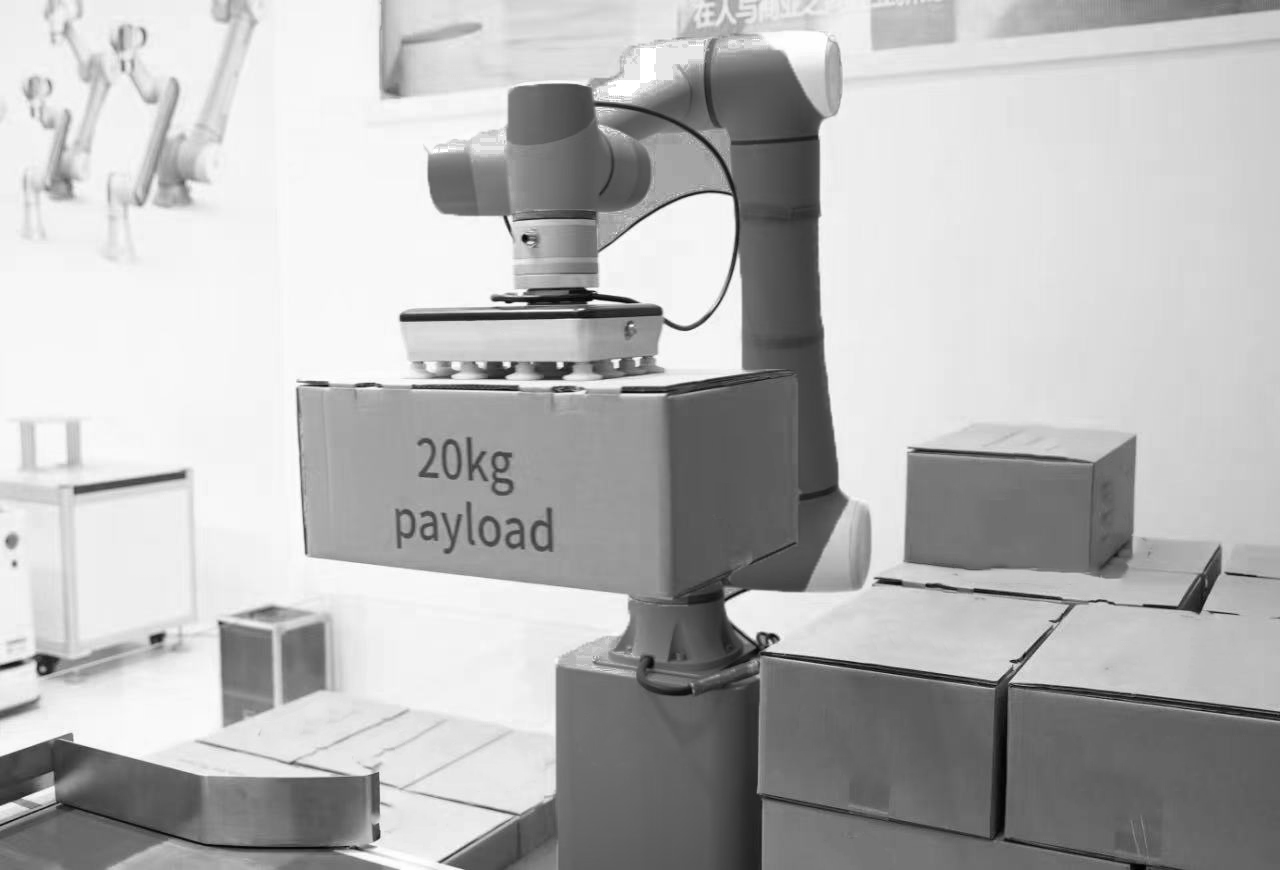
高科技行業自動化案例
痛點:
1)在沒有機器人的情況下人員需要操作四臺機器,進行打螺絲-貼標-測試等工序。
2)工序繁雜且需要長時間站立。
3)人工操作過程中會在每臺設備前積累大量的工件,可能導致現場凌亂,經常拿錯,漏掉其中某個工序直接下線。
4)在缺少員工,導致大批量訂單時,仍需安排白班工人繼續上夜班。
5)考慮到設備使用年限較長,均在十年以上,平時會經常出現故障,如果安全設施出現問題時,容易導致人員受傷。
應用協作機器人自動化優勢:
1)快速替代人工,短時間內升級為自動化方案。
2)無需對原有設備進行改造,機器人可適應原有設備進行規劃與調試。
3)靈活性高,工作方式可通過機器人編程隨意修改,更加方便。
4)機器人可替代原有一個人員,不間斷工作,工作現場整潔有序。
5)機器人與原有設備進行通訊,在每一步都會確認安全信號,發生安全事故的概率降為0。
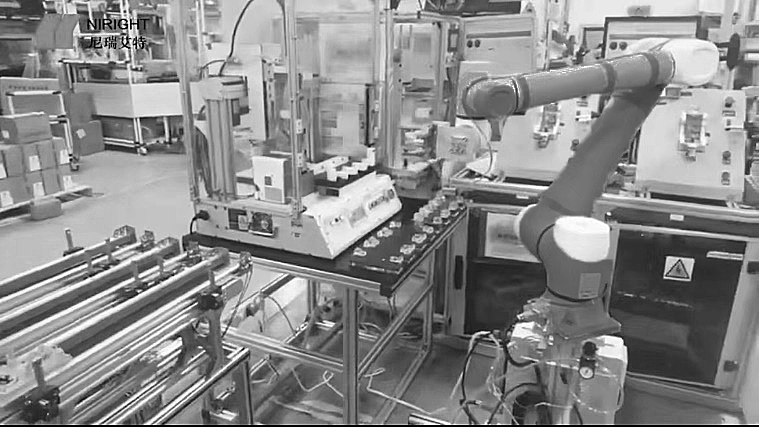